IROS Workshop 2020
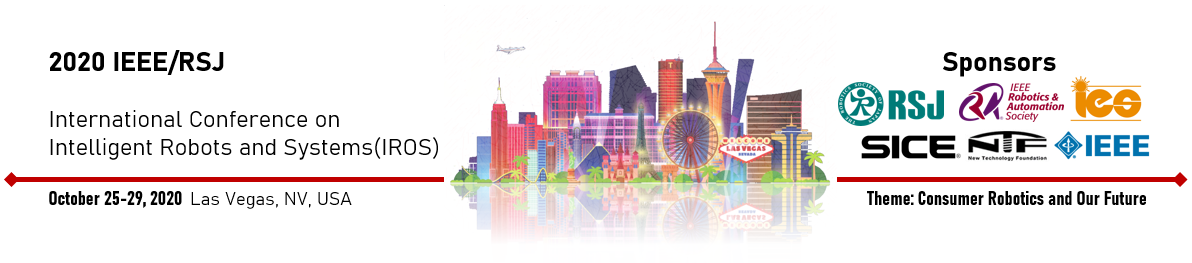
3rd Ergonomic Human-Robot Collaboration: Opportunities and Challenges
October 30th 25th, 2020
NOTIFICATION
We invite you to join the live sessions of IROS 2020 Workshop on “3rd Ergonomic Human-Robot Collaboration: Opportunities and Challenges”:
* Time: 8.00AM - 13.30PM (UTC+1), 30th of October, 2020, Friday
* Location: MS TEAMS Live events (is available as Desktop App, Web App or Mobile App.)
* Website (Live session & QnA): https://short.iit.it/3rdergonomichumanrobotcollaboration
* Introduction on IROS 2020 On-Demand: https://short.iit.it/1w
In many industrial countries, work-related musculoskeletal disorders (WMSD) are associated with high costs to employers such as lost productivity, worker's compensation costs, and so on. WMSD risk factors include awkward posture, repetition, mechanical compression, vibration, etc. To tackle such risk factor, a workplace ergonomics assessment comprises of intervention descriptions for WMSD and the intervention strategy for reducing, eliminating, or controlling worker exposure to the WMDS risk factor. These measures aim to ensure workers' health and safety. Human-Robot Collaboration (HRC) a promising concept that can potentially help with maintaining and improving ergonomics and working conditions of human co-workers. However, the traditional HRC technologies mostly focus safety in terms of collision avoidance and impact safety, while ergonomics potential is largely under-exploited. Therefore some of the major challenges and opportunities to exploit such potential are: collaborative robots have to be aware of co-worker's state and predict his/her actions; the interactive motion has to be able to reconfigure the human working conditions; the methods must operate online.
The above-mentioned challenges and opportunities present a novel research topic for the community. We previously organized two successful workshops to establish the field and to discuss this topic. First, we held a workshop at ICRA 2018 to introduce and discuss the concept in terms of collaborative robotics. Then we held a continuation workshop at IROS 2019 to review the initial research progress based on the goals set at the first workshop and identify major ongoing research problems. Now it is time to discuss those problems and come up with solutions to make progress towards robust and applicable methods for ergonomic human-robot collaboration.
The proposed workshop will first review the progress of the research and development in the new field that was achieved since the last workshop at IROS 2019. Next, we will focus on how to solve the problems that emerged during the research and development based on the goals that were set at the previous workshop. In addition, we will discuss potential novel research directions, ergonomic metric and robot control methods. Finally, we will discuss and design new validation methods that can be used for objective benchmarking within the field. Such an approach requires experts from various research fields and interdisciplinary discussion. For this purpose, we assemble a diverse set of organizers and speakers, who are leading experts in their respective areas that are highly relevant to this workshop topic.
The questions we want to address
-
How to clearly define the measures for ergonomics in human-robot collaboration? - How to design the appropriate optimization that the robot controller can use?
- Are the proposed ergonomic measures sufficient to ensure ergonomic conditions and prevent work-related injuries in terms of bio-medical aspects?
- How to improve the existing modelling of the human and effectively apply it to achieve ergonomic human-robot collaboration?
- Learning algorithms may help the robot to overcome some of the above-mentioned issues.
- What kind of additional sensory feedback systems are required?
- How can robot learning methods be utilized to this end? What are the challenges in achieving the proposed goal in different applications (i.e. industrial human-robot collaboration, wearable robots, service robots, etc.)?
Interests
Physical Human-Robot Collaboration, Human Modelling, Physical Interaction Control, Adaptation and Learning, Industrial Robots, Exoskeleton Robots, Wearable Sensors, Feedback Devices, Shared Control.
Contributions
We will welcome prospective participants to submit extended abstracts (up to 4 pages) to be presented as posters. The manuscripts should use the IEEE IROS two-column format. A PDF copy of manuscript should be submitted through our EasyChair platform. Each paper will receive a minimum of two reviews. The papers will be selected based on their originality, relevance to the workshop topics, contributions, technical clarity, and presentation.
Submission website
[HERE]
Important dates
- Submission deadline for extended abstracts: 1st 21st of September, 2020
- Notification of acceptance: 15th 30th of September, 2020
Speaker instructions
All authors of selected papers are expected to give a short presentation of their paper for 3-5 minutes.
Schedule
Time | Description |
---|---|
08.00 - 08.10 | Introduction by the organizers |
08.10 – 08.40 | Talk 1 by Prof. Dr. Lars Fritzsche |
08.40 – 09.10 | Talk 2 by Prof. Heni Ben Amor |
09.10 – 09.40 | Talk 3 by Dr. rer. nat. Freek Stulp |
09.40 – 10.10 | Talk 4 by Prof. Luka Peternel |
10.10 - 10.20 | Coffee Break |
10.20 – 10.40 | Short paper presentation (3-5min. each) |
10.40 – 11.10 | Talk 5 by Dr. Wansoo Kim and Dr. Arash Ajoudani |
11.10 – 11.40 | Talk 6 by Prof. Bram Vanderborght (Presented by Dr. ir. Ilias El Makrini) |
11.40 – 12.10 | Talk 8 by Dr. Eiichi Yoshida |
12.10 – 12.40 | Talk 9 by Dr. Serena Ivaldi |
12.40 – 13.10 | Round Table Discussions |
Organizers
Wansoo Kim, Post Doc
Italian Institute of Technology, Italy
e-mail: This email address is being protected from spambots. You need JavaScript enabled to view it.
Wansoo Kim is a post-doctoral researcher at Human-Robot Interfaces and Physical Interaction Lab, IIT, Italy. He received the B.S. degree in mechanical engineering from Hanyang University, Korea in 2008 and a Ph.D. degree in mechanical engineering from Hanyang University, Korea in 2015 (Integrated MS/PhD program). He has developed several exoskeleton systems such as HEXAR-Hanyang Exoskeleton Assistive Robot, and conducted research on the control of the powered exoskeleton robot through the physical human-robot interaction (pHRI) forces. He is currently involved in a project Horizon-2020 project SOPHIA. He has contributed to several projects in the field of exoskeleton robot in Korea projects (High responsive control technology of a lower-limb exoskeleton under rough terrain-1415144732, Development of Wearable Robot for Industrial Labor Support-1415135223, etc.), and joint R&D projects with a company (DSME and LIG Nex1). He was the winner of the Solution Award 2019 (Premio Innovazione Robotica at MECSPE2019), the winner of the KUKA Innovation Award 2018, the winner of the HYU best PhD paper award 2015, and the winner of the ICCAS best presentation award 2014. His research interests are in Physical human-robot interaction (pHRI), human-robot collaboration, Shared Control, Ergonomics, Human modelling, Feedback devices, and powered exoskeleton robot.
Luka Peternel, Assistant Professor
Delft University of Technology, Netherlands
e-mail: This email address is being protected from spambots. You need JavaScript enabled to view it.
Luka Peternel received a Ph.D. in robotics from Faculty of Electrical Engineering, University of Ljubljana, Slovenia in 2015. He conducted Ph.D. studies at Department of Automation, Biocybernetics and Robotics, Jožef Stefan Institute in Ljubljana from 2011 to 2015, and at Department of Brain-Robot Interface, ATR Computational Neuroscience Laboratories in Kyoto, Japan in 2013 and 2014. He was with Human-Robot Interfaces and Physical Interaction Lab, Advanced Robotics, Italian Institute of Technology in Genoa, Italy from 2015 to 2018. From 2019, Luka Peternel is an Assistant Professor at Department of Cognitive Robotics, Delft University of Technology in the Netherlands.
Arash Ajoudani, Principal Investigator
Italian Institute of Technology, Italy
e-mail: This email address is being protected from spambots. You need JavaScript enabled to view it.
Arash Ajoudani received his PhD degree in Robotics and Automation from Centro "E Piaggio", University of Pisa, and Advanced Robotics Department (ADVR), Italian Institute of Technology (IIT), Italy (July 2014). His PhD thesis was a finalist for the Georges Giralt PhD award 2015 - best European PhD thesis award in robotics. He is currently a tenure-track scientist and the leader of the Human-Robot Interfaces and Physical Interaction (HRI2) lab of the IIT. He was a winner of the Amazon Research Awards 2019, the winner of the Werob best poster award 2018, winner of the KUKA Innovation Award 2018, a finalist for the best conference paper award at Humanoids 2018, a finalist for the best interactive paper award at Humanoids 2016, a finalist for the best oral presentation award at Automatica (SIDRA) 2014, the winner of the best student paper award and a finalist for the best conference paper award at ROBIO 2013, and a finalist for the best manipulation paper award at ICRA 2012. He is the author of the book "Transferring Human Impedance Regulation Skills to Robots" in the Springer Tracts in Advanced Robotics (STAR), and several publications in journals, international conferences, and book chapters. He is currently serving as the executive manager of the IEEE-RAS Young Reviewers' Program (YRP), chair and representative of the IEEE-RAS Young Professionals Committee, and co-chair of the IEEE-RAS Member Services Committee. He has been serving as a member of scientific advisory committee and as an associate editor for several international journals and conferences such as IEEE RAL, Biorob, ICORR, etc. His main research interests are in physical human-robot interaction and cooperation, robotic manipulation, robust and adaptive control, rehabilitation robotics, and tele-robotics.
Eiichi Yoshida, Co-Director
National Institute of Advanced Industrial Science and Technology (AIST), Japan
e-mail: This email address is being protected from spambots. You need JavaScript enabled to view it.
Eiichi Yoshida received M.E and Ph. D degrees on Precision Machinery Engineering from Graduate School of Engineering, the University of Tokyo in 1993 and 1996 respectively. In 1996 he joined former Mechanical Engineering Laboratory, later reorganized as National Institute of Advanced Industrial Science and Technology (AIST), Tsukuba, Japan. He served as Co-Director of AIST/IS-CNRS/ST2I Joint French-Japanese Robotics Laboratory (JRL) at LAAS-CNRS, Toulouse, France, from 2004 to 2008. Since 2009, he has been serving as Co-Director of CNRS-AIST JRL (Joint Robotics Laboratory), IRL at Tsukuba, Japan, and appointed as Director since 2017 to date. He also served as Deputy Director of Intelligent Systems Research Institute (IS-AIST) from 2015 to 2018 and as Director of Planning Office, Department of Information Technology and Human Factors from 2018 to 2020, at AIST. He is currently Deputy Director of Industrial Cyber-Physical Systems Research Center, and TICO-AIST Cooperative Research Laboratory for Advanced Logistics in AIST. He was awarded Chevalier, l’Ordre National du Mérite from French Government in 2016 for his long-term contributions to French-Japanese collaboration on robotics. He is IEEE Fellow, and member of RSJ and JSME. His research interests include robot task and motion planning, human modeling, humanoid robots and advanced logistics technology.
Invited Speakers
-
Dr. Wansoo Kim
Istituto Italiano di Tecnologia, Italy“Ergonomic control of human-robot coexistence and collaboration”
The talk will present a control approach to human-robot co-manipulation that accounts for human ergonomics and related fatigues. We will first present a human monitoring method that includes a overloading joint torque estimation technique, as well as the feedback methods to provide a guidance to human. The robot by means the mobile manipulator platform MObile Collaborative robotic Assistant (MOCA) then uses the lower level control framework in conjunction with the proposed higher level methods that can anticipate human ergonomic states. The robot then uses the proposed methods to control its own behaviour in a way that offloads the excessive effort of the human and ensures ergonomic working conditions, as well as the coexistence in the workplace. -
Prof. Luka Peternel
Delft University of Technology, Netherlands"Ergonomics in Human-Robot Co-Manipulation Control"
The talk will present several robot control methods for co-manipulation with humans, where the key element is an optimisation of human ergonomics. The optimization process incorporates biomechanical models and real-time measurements to track and improve various metrics, such as: muscle fatigue, joint torques and arm manipulability. In the first part, the focus is on the application to co-manipulation during physical human-robot collaboration in various practical tasks (e.g., collaborative sawing, polishing, valve turning, etc.). The second part will focus on the application in exoskeletons, where co-manipulation is done while human and robot limbs are physically coupled. Finally, the last part will examine the application in teleoperation, where co-manipulation pertains to the remote robot being commanded by a human operator. In particular, we will present an analysis of impedance-command interfaces in force-feedback tele-impedance. -
Dr. Eiichi Yoshida
National Institute of Advanced Industrial Science and Technology (AIST), Japan"Human-Centered Behavioral Analysis for Human-Robot Cooperation"
Demands are increasing for robots that can cooperate with humans more naturally and comfortably. We have been conducting research on human-centered analysis focusing on observation of humans' reaction when doing cooperative tasks with a robot. We first analyzed factors causing discomfort, and experiments in a coworker scenario implied that perceived uncertainty in a robot’s movement is a key determinant of how much humans are comfortable with them due to robot motion uncertainty. Through another task of handover, we have found that humans are combining feedforward and feedback control, whose parameter varies depending on personality and physical dimensions. Finally, we are conducting studies on active physical human-robot cooperation. In a physically cooperative task scenario, we obtained first results on factors alternating humans' behavior when the robot interacts actively with them. We will keep addressing design principle of behavior of future collaborative robots by reinforcing those experimental studies with increased involvement of robots. -
Dr. Serena Ivaldi
National Institute for Research in Computer Science and Control (Inria), France"Prediction and optimization for ergonomics movement in human-robot collaboration"
In this talk I will present our recent results in prediction of human movement for improving human-robot collaboration and optimization of human movement with respect to ergonomics criteria. -
Dr. ir. Ilias El Makrini / Prof. Bram Vanderborght
Vrije Universiteit Brussel, Brussels, Belgium"Improving workers’ ergonomics by cobots and exoskeletons"
Cobots allow to combine the dexterity, flexibility and problem-solving ability of humans, with the strength, endurance, quality consistency and precision of robots and can be redeployed to other tasks much more easily. By also placing health, the working conditions and the sustainable development goals central, we can ensure ourselves to reap the full benefits not only economically but also for our society. This talk will discuss the multidisciplinary approach to develop a new generation of cobots and exoskeletons and control algorithms for improving the ergonomics of workers in the manufacturing industry. -
Dr. rer. nat. Freek Stulp
Institute of Robotics and Mechatronics, German Aerospace Center (DLR), Germany"Human-Robot Collaboration: From Low-Level Learning to High-Level Planning" In this talk I first present our work on using machine learning to “compile” complex biomechanical simulations into compact models which can be quickly queried. These models are used to optimize robotic behavior with respect to relevant musculo-skeletal variables of humans that physically interact with the robot. In our current work, we are applying this approach to compensating for the so called “limb position effect” in prosthetic control. Finally, I will provide an outlook on using high-level planning to automatically distribute tasks between robots and humans, which aim at factory-wide optimization, rather than the behavior of individual robots.
-
Prof. Heni Ben Amor
Arizona State University, USA"Predictive Biomechanics for Ergonomic Control in Human-Robot Interaction"
How can robots physically interact with humans in a meaningful and healthy way? Existing approaches to specifying close-contact, physical interactions between humans and robots focus solely on successful task completion. However, these approaches completely neglect the biomechanical and ergonomic ramifications of robot actions on the human body. An action which may seem momentarily effective may result in stresses to the human musculoskeletal system and even serious injuries. In this talk, I will discuss how machine learning enables healthy, bi-directional, and biomechanically-safe interactions between humans and machines that can be sustained over long periods of time. Specifically, I will present Bayesian Interaction Primitives -- a probabilistic framework that enables learning and inference for HRI scenarios. Bayesian Interaction Primitives encode the mutual dependencies between interaction partners and can be used to 1.) predict human motion and sensor values, 2.) infer task-relevant biomechanical variables, and 3.) generate appropriate robot responses. Used within a model-predictive control loop, Bayesian Interaction Primitives generate actions that minimize long-term impact on the musculoskeletal system of the human partner. To demonstrate the approach, I will present a number of applications in prosthetics and social robotics. -
Prof. Dr. Lars Fritzsche
imk automotive GmbH, Germany"3D simulation and validation of collaborative work systems – Safety, ergonomics and productivity assessment with “ema Work Designer” "
Using collaborative robots (“cobots”) for supporting work tasks with high physical and psychological demands (“un-ergonomic tasks”) is a very promising approach for compensating the aging workforce in Europe and improving health and productivity in the industrial sector. However, it is not easy to design collaborative work systems according to safety, ergonomics and productivity standards from a technical and a social point of view. Many details of the applied technologies have to be taken into account and workers should be allowed to participate in the work system design proactively in order to consider their practical knowledge and increase their acceptance for the implemented solution. “ema Work Designer” is a software tool that enables to design manual and semi-automatic (= collaborative) work systems according to safety, ergonomics and productivity standards like DIN ISO/TS 15066, EAWS and MTM. The interactive 3D visualization supports technical experts in work station design and facilitates communication with workers. This presentation will show a use case that was developed in the EU-founded SOPHIA-Project with the company Hankamp Gears. Based on the current manual work station, a solution for integrating the UR16e cobot was designed as a collaborative work system together with technology specialists, social scientists and representatives from the target company. ema Work Designer software was used to validate the geometrical set-up of the work station in interaction with the cobot platform. Moreover, it was used to assess the performance of the current and the future work system, for example showing a reduction of active manual production time (measured with MTM) by 18 seconds/cycle (= -28%) and ergonomic work load (measured with EAWS) by 31,5 points (= -59%).
Acknowledgments
The following IEEE-RAS Technical Committees have acknowledged the full support of the proposed workshop:
Sponsorship
This workshop will be supported by the European Union’s Horizon 2020 research and innovation program under grant agreement No. 871237 (SOPHIA), and from the European Research Council program under grant agreement No. 850932 (Ergo-Lean). The project SOPHIA will support a USB-key, which includes the workshop proceedings and the introduction of the SOPHIA project, for the attendees. The organisers are also evaluating the possibility of a post workshop social event (e.g. dinner) funded by the project (Ergo-Lean).